4 Features and 5 Applications of Vacuum Forming ABS Plastic Sheet
14/07/2021Vacuum Forming ABS Plastic Sheet is an emerging material in the sheet industry. Its full name is acrylonitrile/butadiene/styrene copolymer sheet, and it is the most widely used polymer with the largest production volume. It organically unifies the various properties of PS, SAN, and BS, and has excellent mechanical properties of toughness, rigidity, and stiffness in balance.
Vacuum Forming ABS Plastic Sheet has 4 main characteristics.
1, has excellent mechanical properties. ABS has excellent impact strength and can be used at very low temperatures; ABS has excellent wear resistance, good dimensional stability, and oil resistance, and can be used for bearings under medium loads and rotational speeds.
ABS is not affected by water, inorganic salts, alkalis and acids, but is soluble in ketones, aldehydes and chlorinated hydrocarbons, and is subject to stress cracking by ice acetic acid and vegetable oil.
3, excellent impact strength, good dimensional stability, dyeing, good molding and machining, high mechanical strength, high stiffness, low water absorption, good corrosion resistance, simple connection, non-toxic and tasteless, excellent chemical properties and electrical insulation properties. It can be heat resistant without deformation, and also has high impact resistance toughness in low temperature conditions. Still a hard, not easy to scratch, not easy to deformation of the material. Low water absorption; high dimensional stability. Conventional ABS sheet is not very white, but very good toughness, can be cut with shears, but also can open the mold punch.
The heat deformation temperature of Vacuum Forming ABS Plastic Sheet is 93~118℃, and the product can be increased by about 10℃ after annealing treatment. Among them, transparent ABS sheet has very good transparency and excellent grinding and polishing effect, which is the preferred material to replace PC sheet. Compared with acrylic, it is very tough and can meet the detailed processing of products.
Vacuum Forming ABS Plastic Sheet's 5 major applications
Vacuum Forming ABS Plastic Sheet can be used as the shell and internal components of TV, radio, washing machine, refrigerator, telephone, air conditioner and other electrical appliances.
2、Automotive parts. Vacuum Forming ABS Plastic Sheet is used to make auto parts, such as shells, adjustment handles, door liners, control switch knobs, conduits, etc. The main use of ABS impact resistance, such as strength, stiffness and formability. Accessories are fenders, armrests, ventilation cover, support, cushion extension plate, etc.
3、Office equipment. The use of ABS sheet excellent impact resistance, excellent rigidity, dimensional stability and formability, used to manufacture a variety of office equipment shell both economical and practical. Such as fax machines, copiers, typewriters and computer monitors and other office equipment, fire prevention higher requirements, so the general flame retardant ABS for the order of merit.
4, mechanical ABS plastic shells can be used to produce mechanical equipment and general mechanical parts. Such as water tanks, the appearance of the shell, electrical cabinets, battery cans, gear bearings, pump impeller mold models and fasteners, bolts, covers.
5、Mold model. Due to the superior processing properties of ABS plastic, light specific gravity, low price, in recent years has been widely used in the manufacture of home appliances industry, automotive, machinery and equipment, testing equipment mold model. The current global leader in the use of ABS as a standard material for the production of three-dimensional prototypes, then you can do anything you want to test the appearance of new products modeling, suitability and related functions model flyer size of the machine. It has the best performance to price ratio in its class.
Production process of Vacuum Forming ABS Plastic Sheet.
ABS sheet production process can be divided into upstream and downstream processes.
Upstream process refers to melting, casting, hot rolling, cold rolling, etc., which are the same as those of other high precision sheets and strips.
The downstream process refers to heat treatment, surface treatment, drawing, bending and straightening, lubricant coating, longitudinal and transverse shearing, precision cutting and deep processing, etc. Its downstream process is much more complicated than other high-precision sheet and process is also much more. It can be briefly expressed as: uncoiling - heat treatment, gas cushion furnace (available fuel, electric or induction heating) solution treatment (temperature 500~600℃) or annealing, water quenching / air quenching - surface treatment (cleaning and transformation treatment) - bending palanquin - lubrication coating - winding, etc.
Finally, the difference between Vacuum Forming ABS Plastic Sheet and PVC sheet
1, raw materials: ABS sheet is acrylonitrile / butadiene / dumb vinyl copolymer sheet; PVC sheet is a vacuum blister film.
2、Application: ABS sheet is widely used in food industry parts, architectural model, hand board production, into phase electronic industry parts, refrigerator refrigeration industry, electronic and electrical fields, pharmaceutical industry, auto parts, etc.; PVC sheet is widely used in chemical industry, petroleum, electroplating, water purification treatment equipment, environmental protection equipment, mining, medicine, electronics, communication and decoration, etc.
ABS sheet is acrylonitrile/butadiene/stupid vinyl copolymer sheet; PVC sheet is a kind of vacuum blister film.
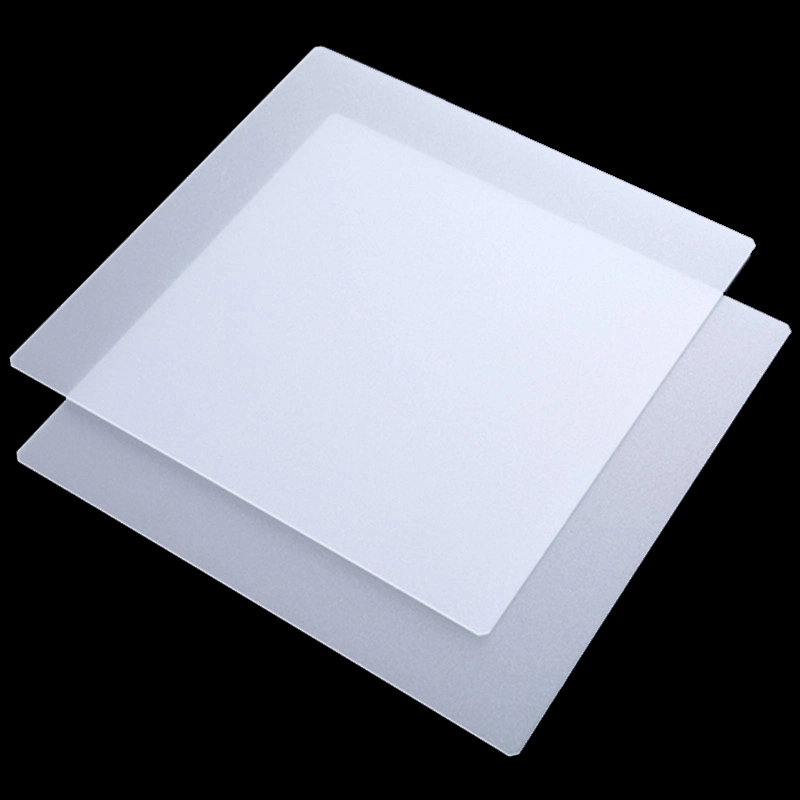
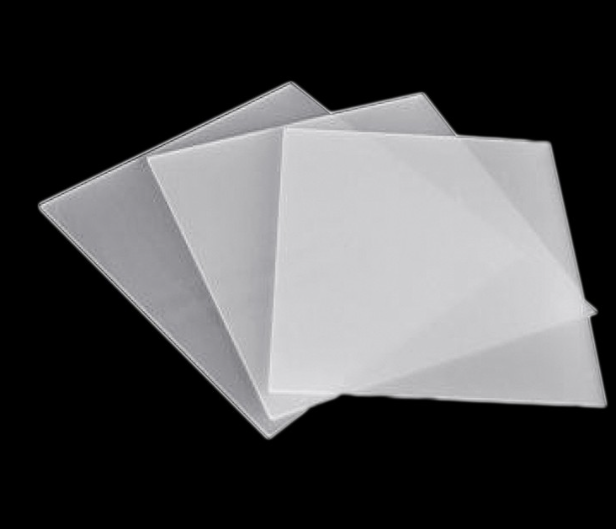
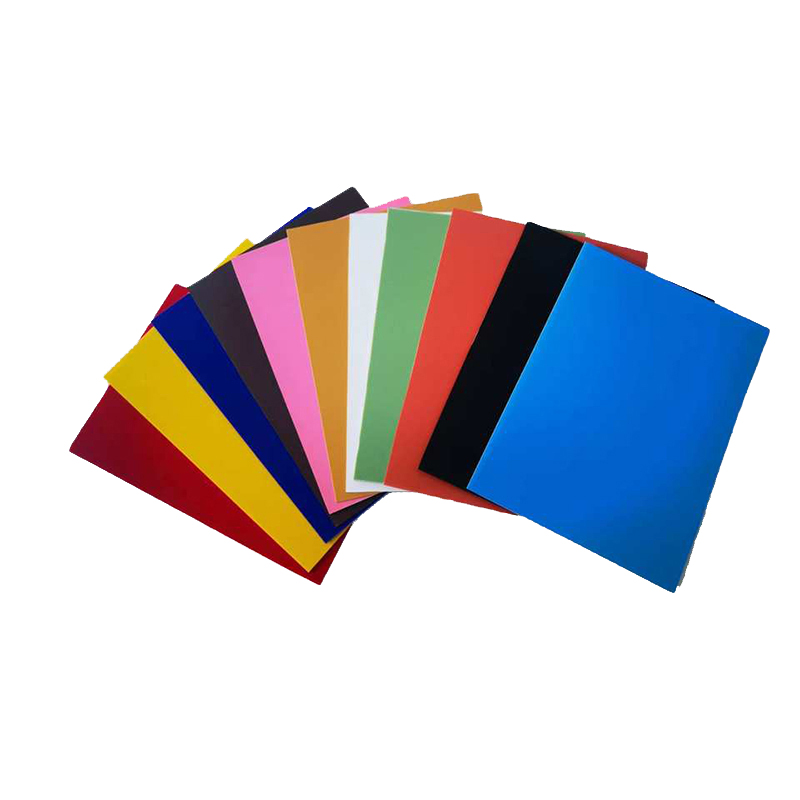
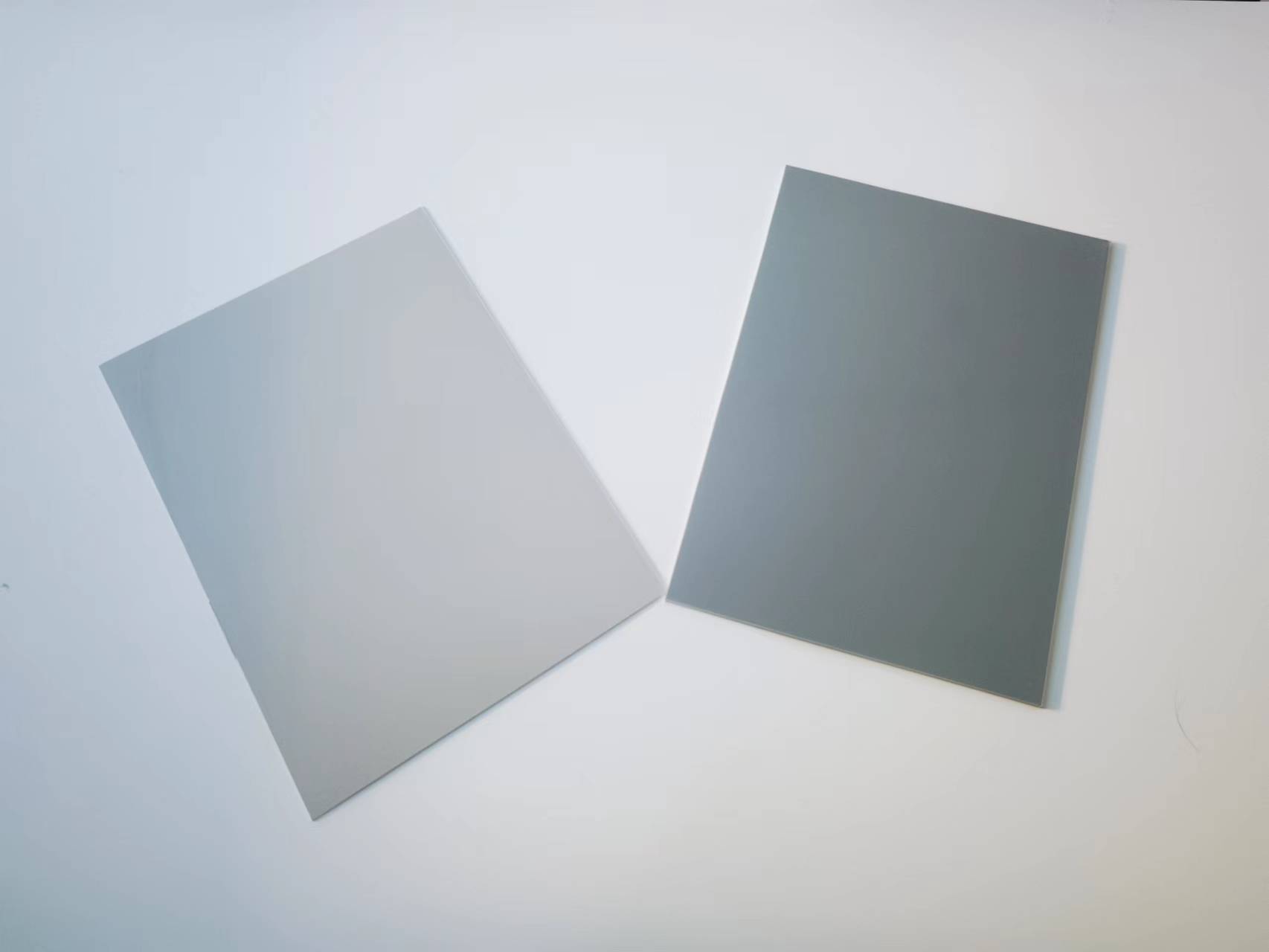
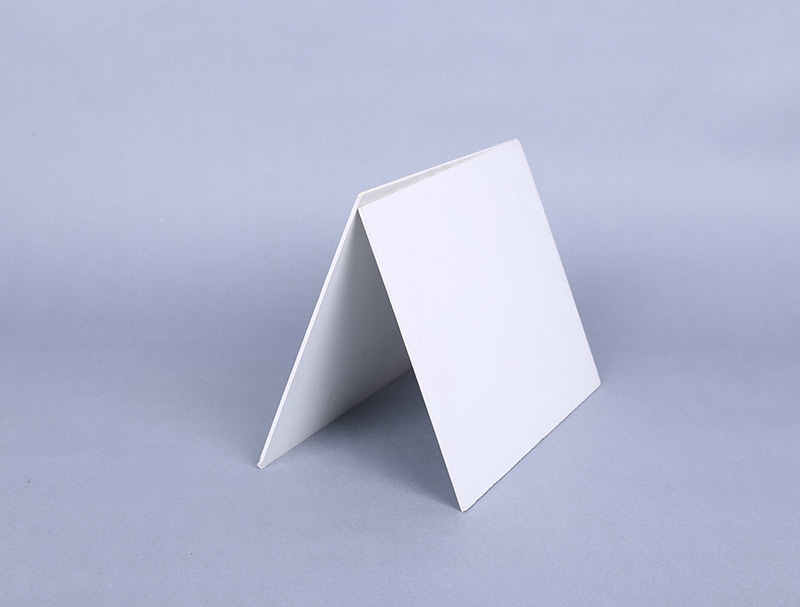
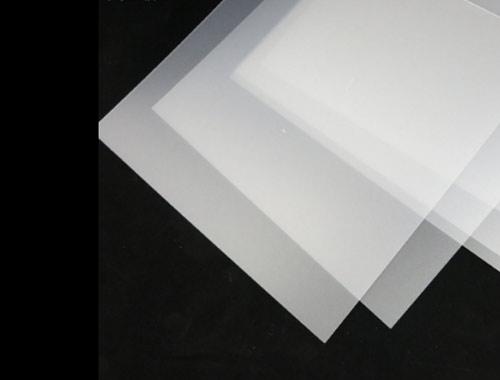